Hubei Xianghua Machinery | Lean Improvement in Action (Part 1)
Classification: Company Dynamics
Time2025-01-08
In July 2024, Hubei Xianghua Machine held the kick-off meeting for the Lean Benchmark Factory Planning Project, marking the beginning of lean management. Through continuous exploration and practice, Hubei Xianghua Machine focuses on eliminating the "eight wastes," the "eight protections" of equipment maintenance, and the "6S management" of the production site, driving the company to innovate and create value continuously. The Hubei Xianghua Machine WeChat public account has specially set up a column to report on outstanding lean improvement results.
Since the launch of the Lean Benchmark Factory Planning Project, Hubei Xianghua Machine has focused on TPM management, lean improvement of the eight wastes, and continuous improvement of site management, achieving good results.
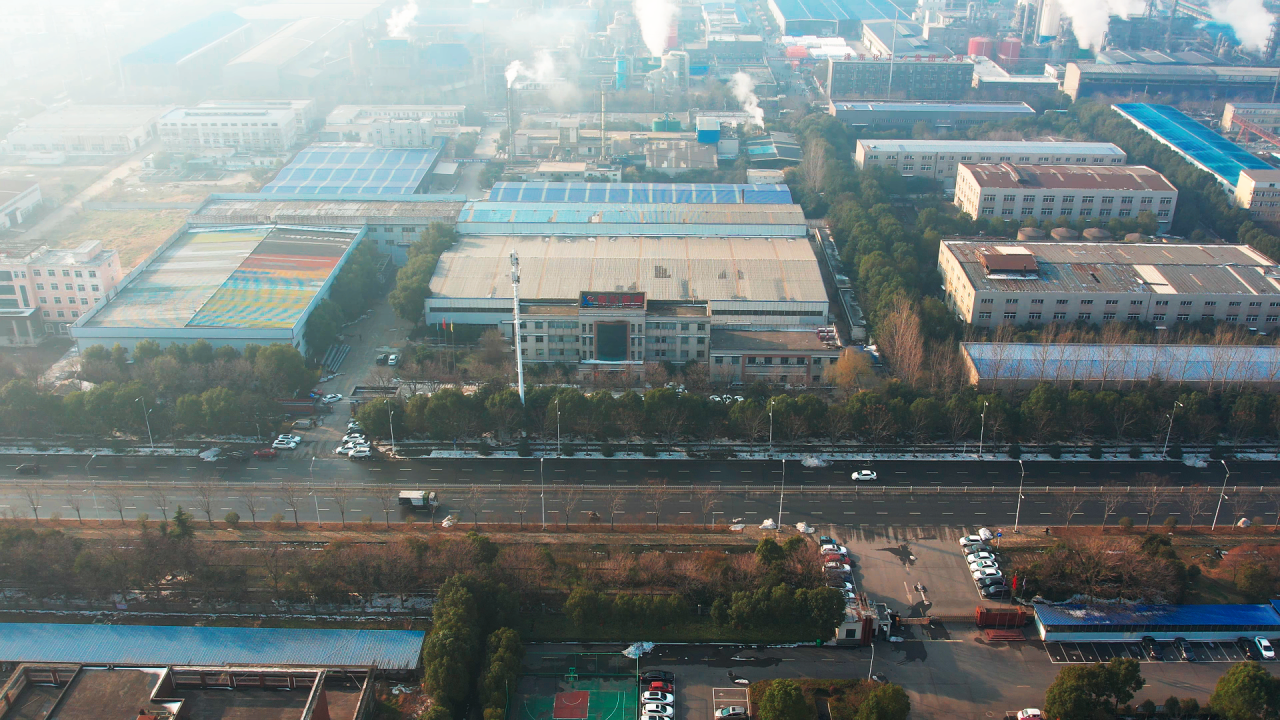
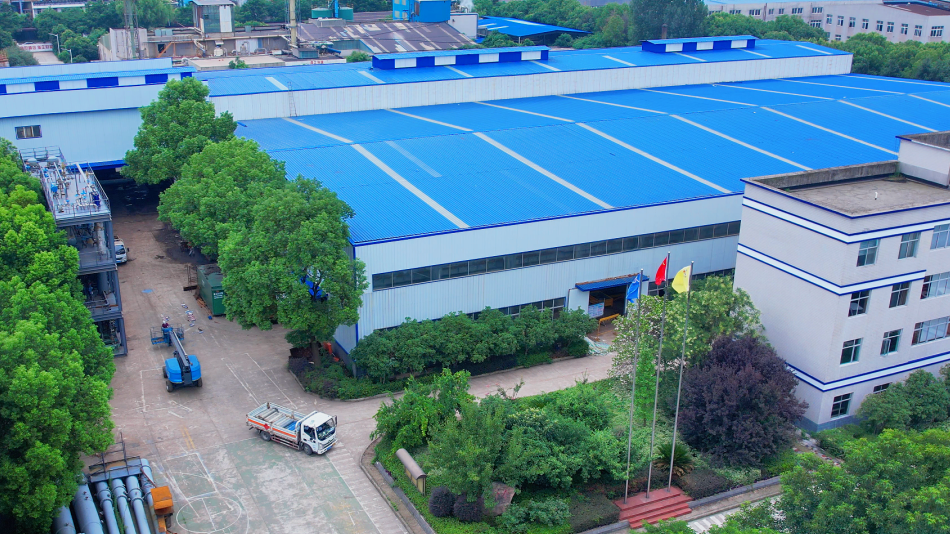
▲ The factory's roof and sides have been completely replaced with new materials that have better corrosion resistance, creating a solid barrier for the workshop.
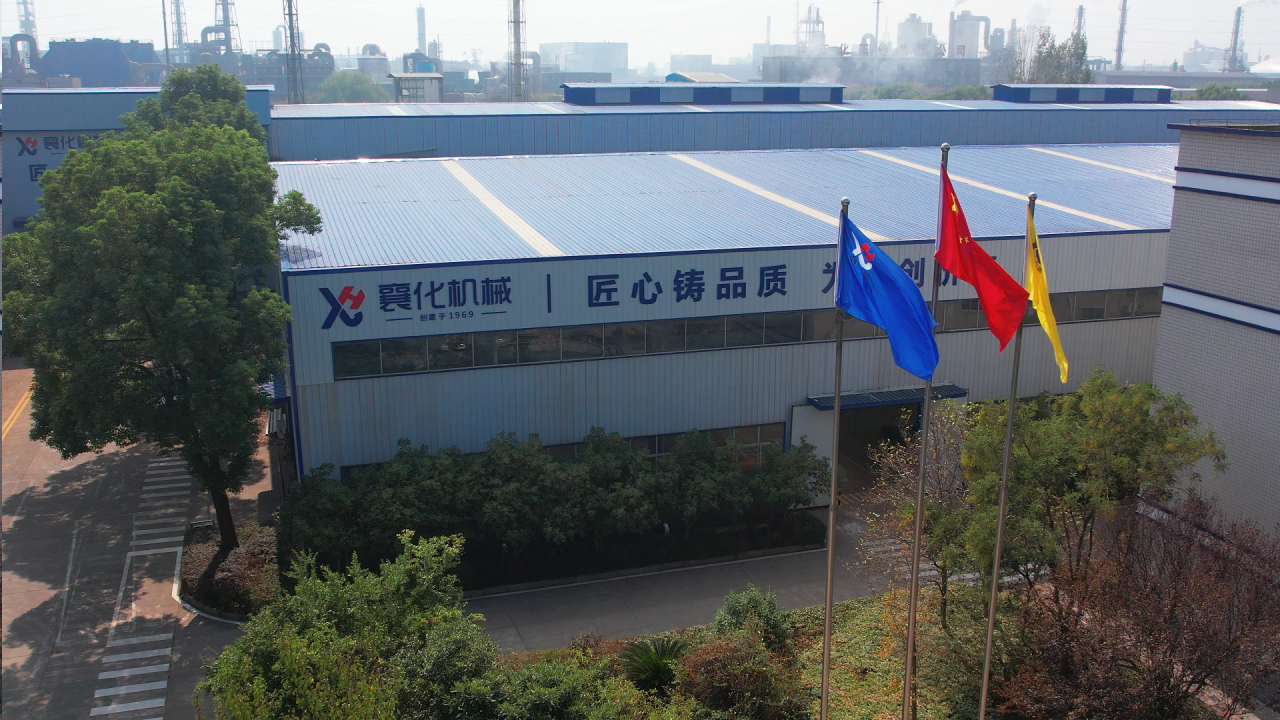
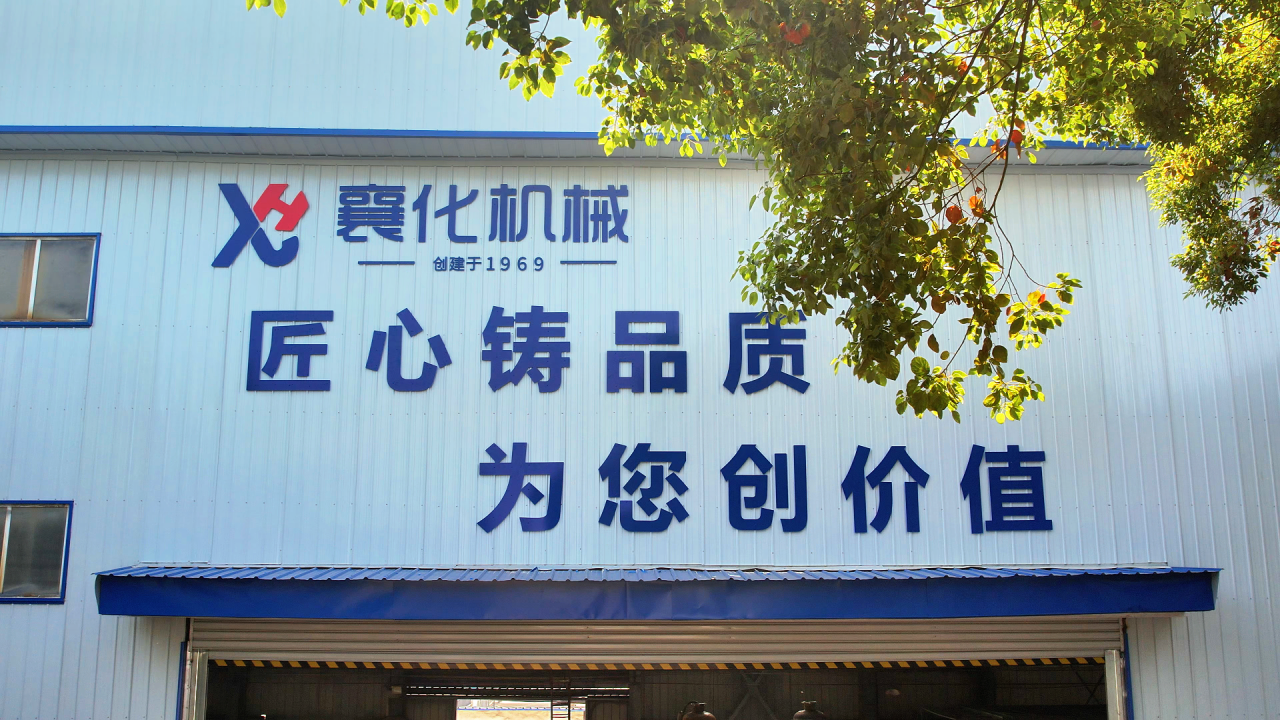
▲ The factory's roof and sides have been completely replaced with new materials that have better corrosion resistance, creating a solid barrier for the workshop.
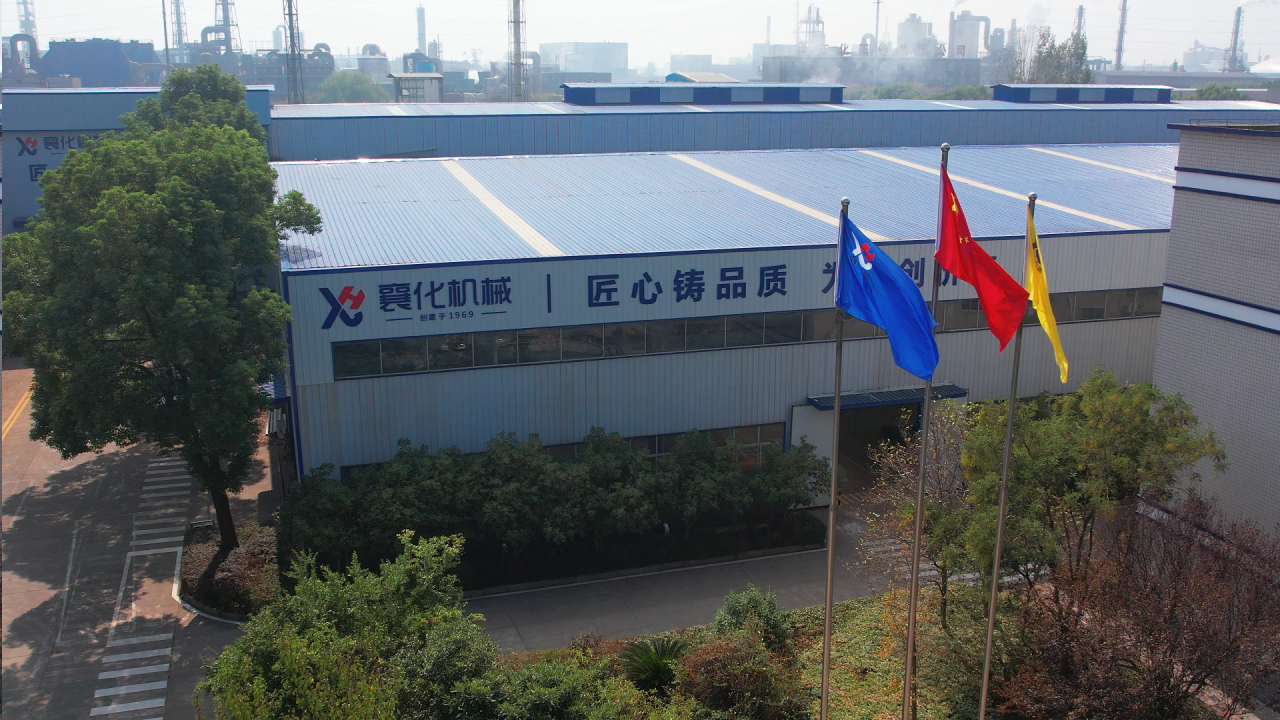
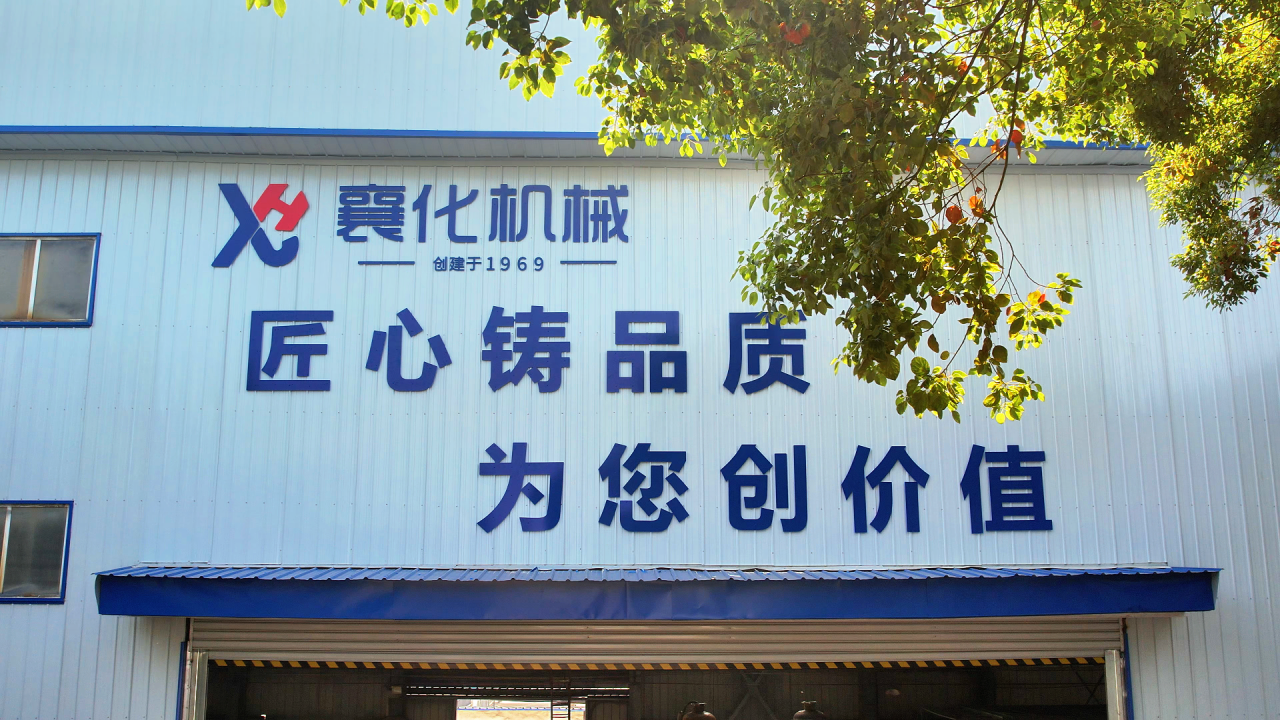
▲ The customer service philosophy is displayed on the wall, embedding the corporate culture in everyone's heart.
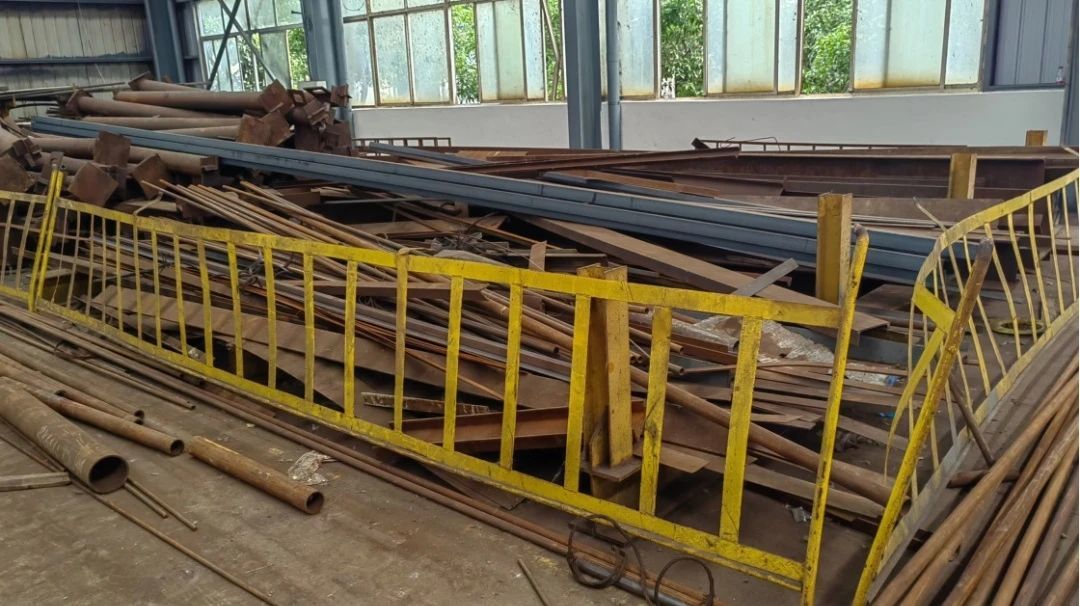
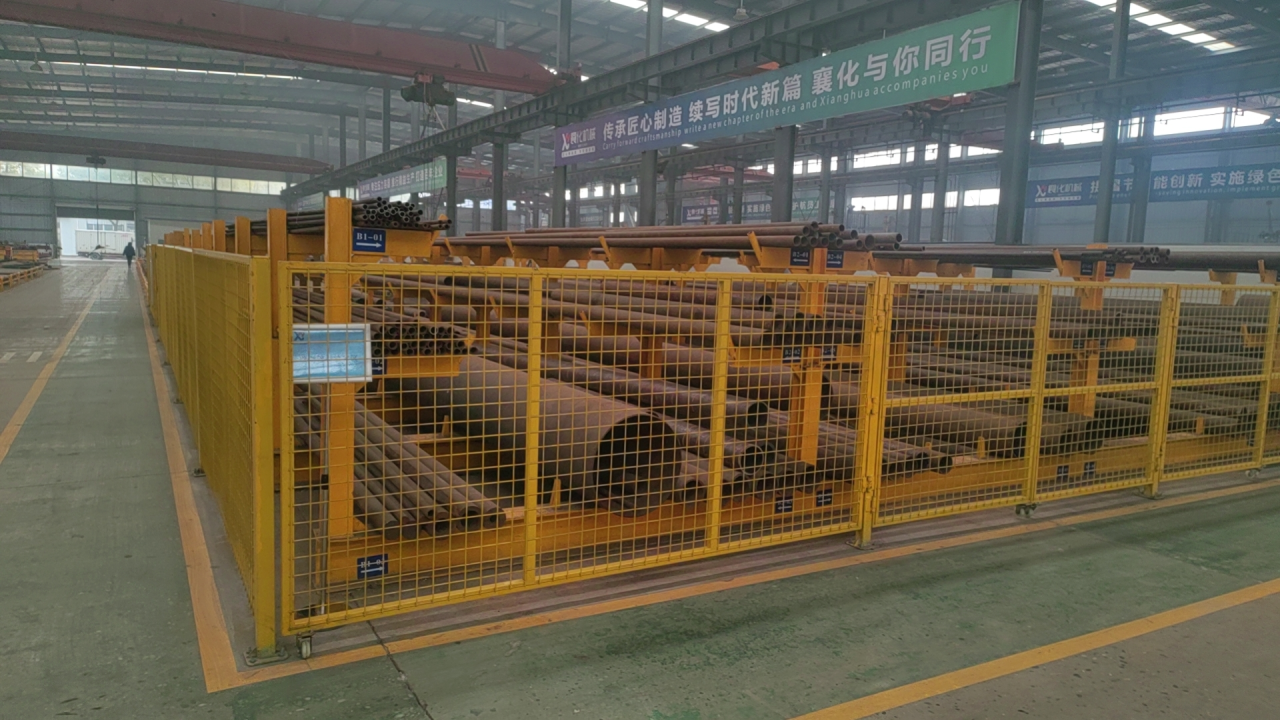
▲ The pipe and profile storage area has been organized, with layered racks made for different materials and models placed in different areas, labeled effectively to solve the "difficulty in finding materials" problem.
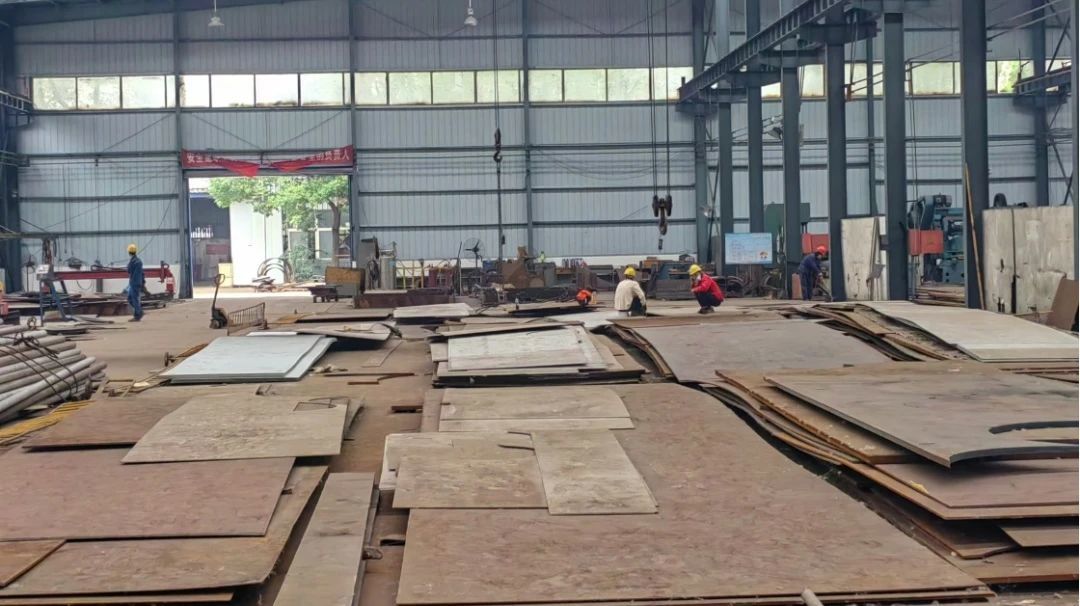
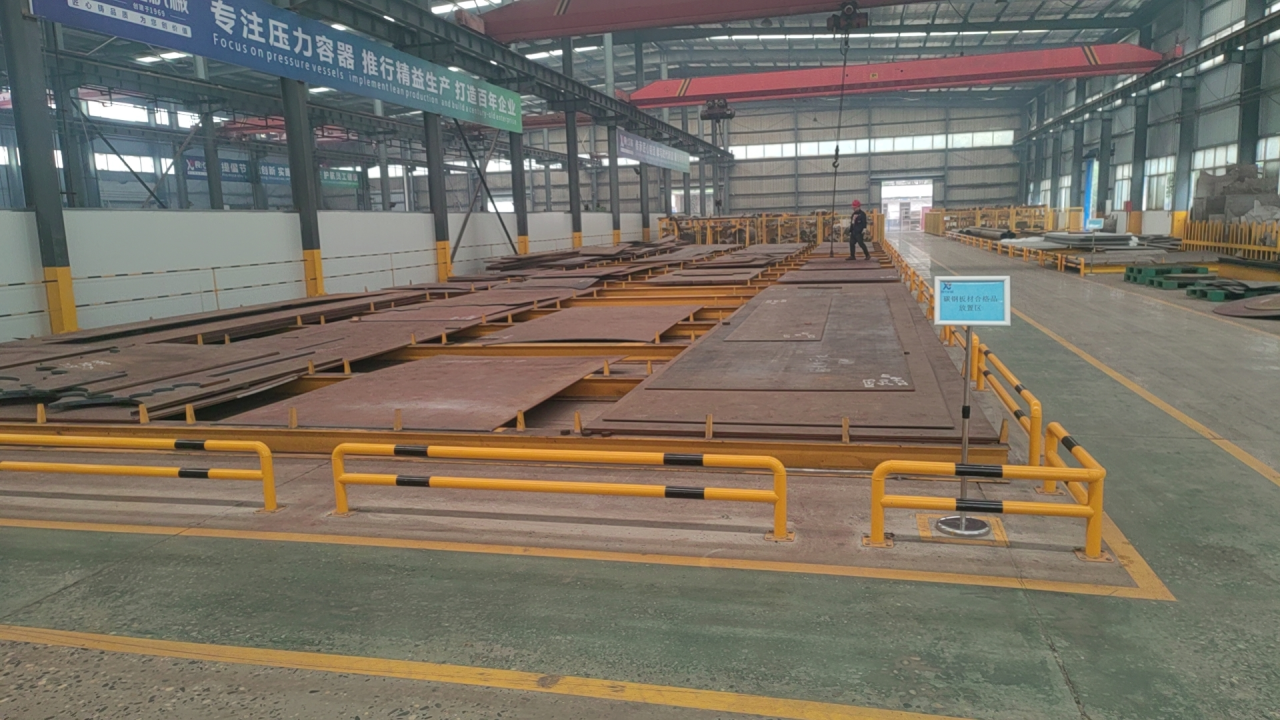
▲ In strict accordance with the material management requirements for pressure vessels, the carbon steel plate area and stainless steel plate area have been separated, and a method of "full coverage with I-beams and positioning blocks" has been adopted to divide small storage areas based on material and thickness, with clear labeling, greatly improving cutting efficiency.
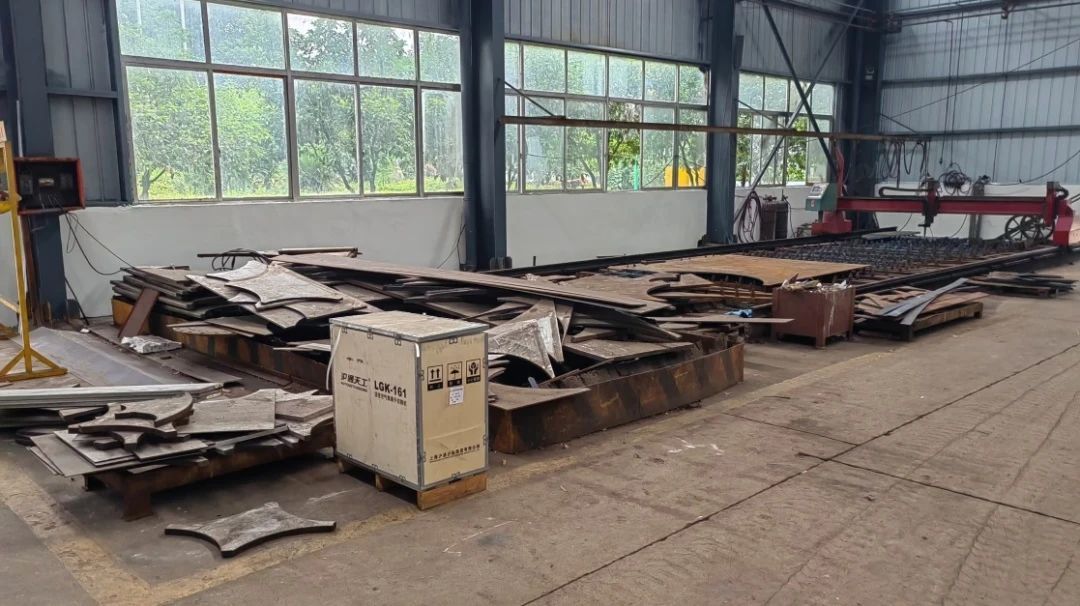
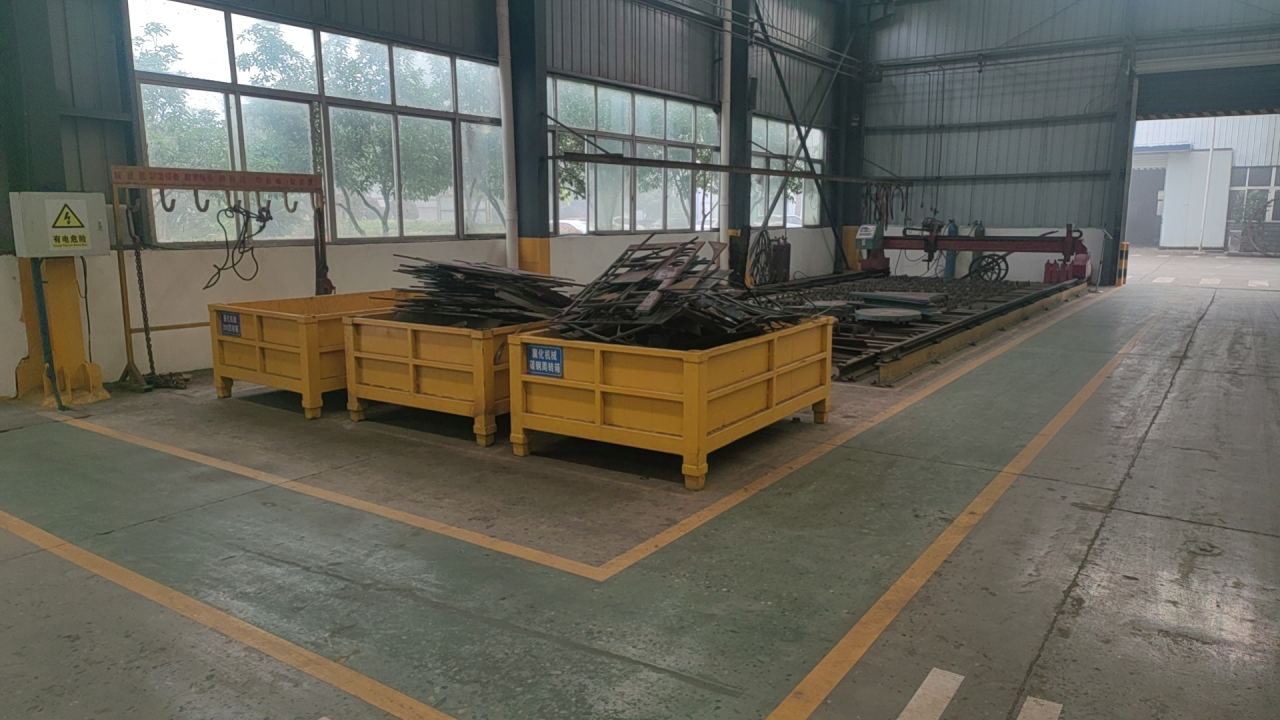
▲ By creating waste placement boxes and categorizing waste, safety hazards have been eliminated, and the working environment in the cutting area has improved.
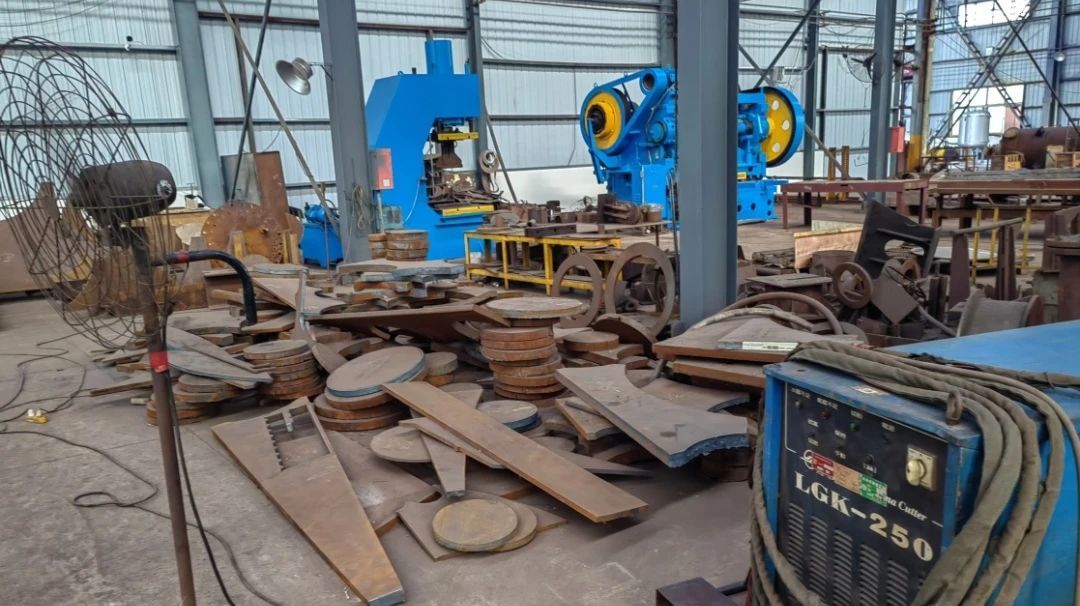
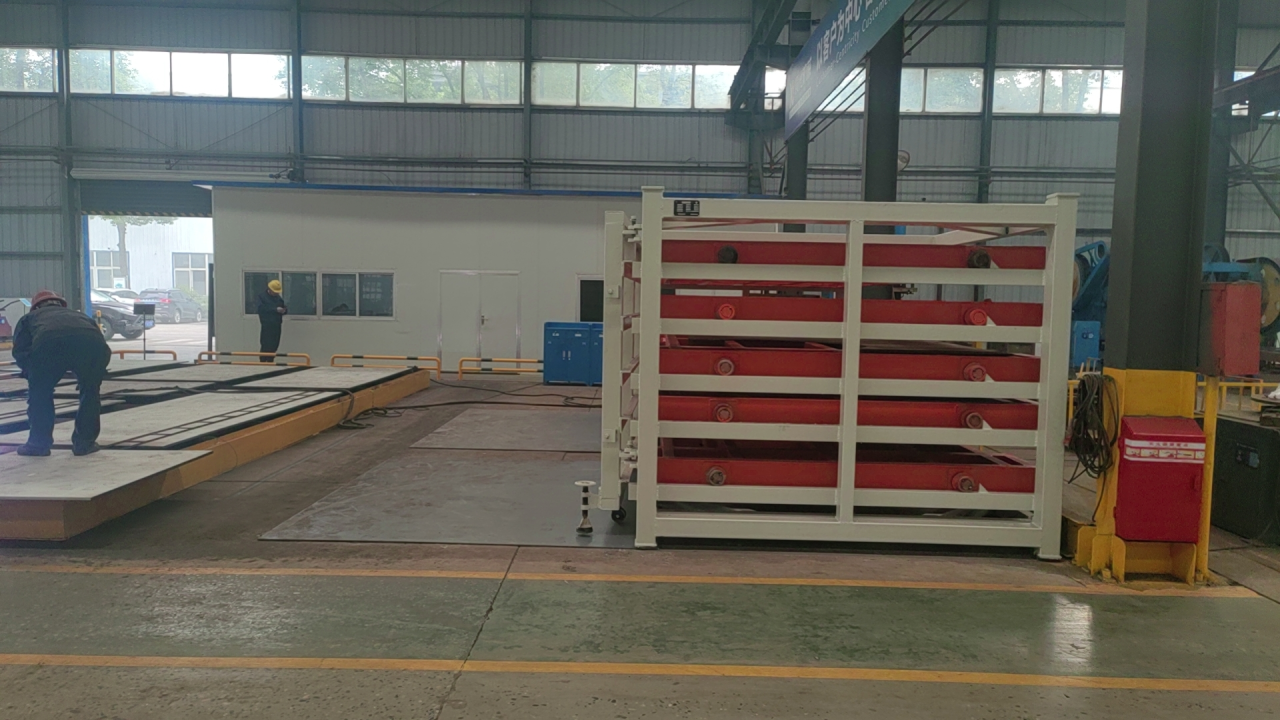
▲ The use of drawer-type edge material racks saves space, significantly reduces time waste, and enhances the workshop's aesthetics, achieving three benefits in one.
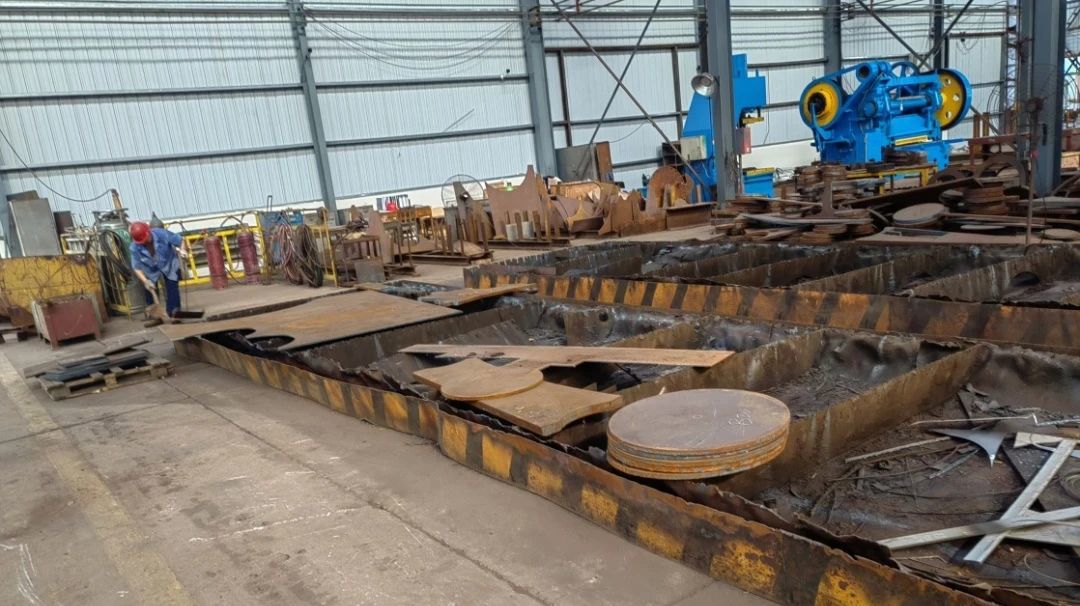
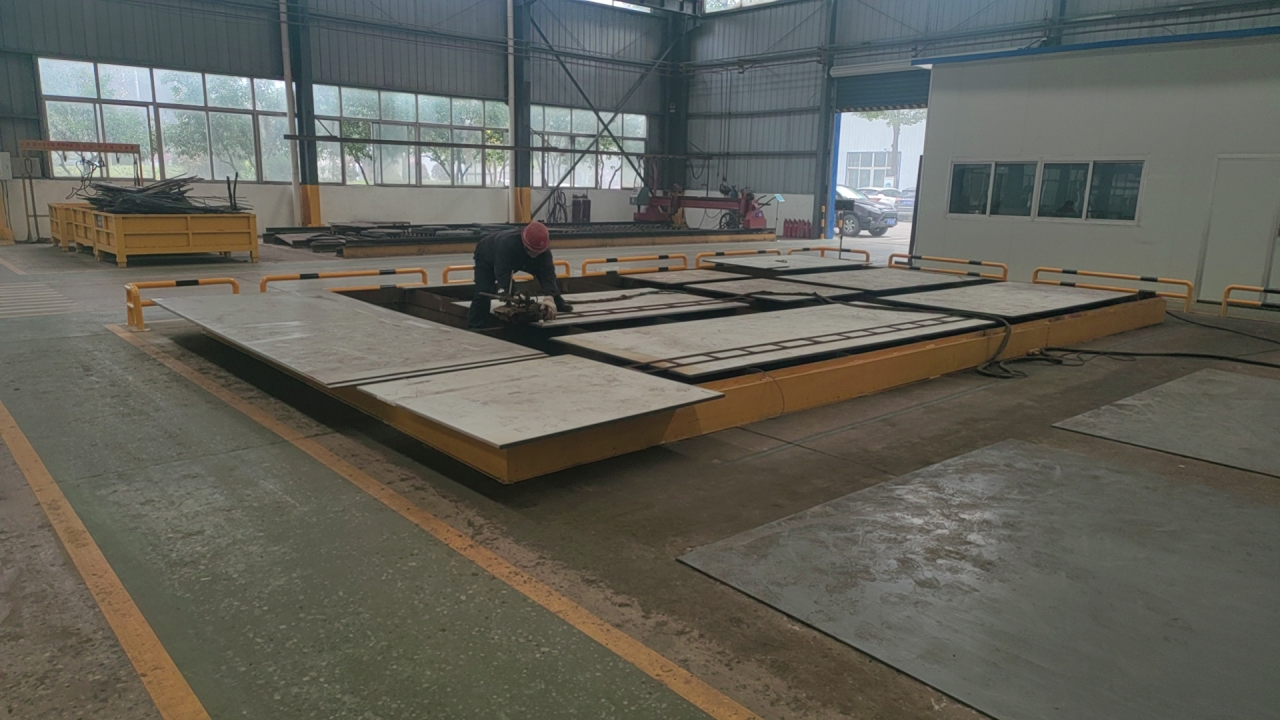
▲ The newly made cutting trough is beautiful and atmospheric, making a striking impression.
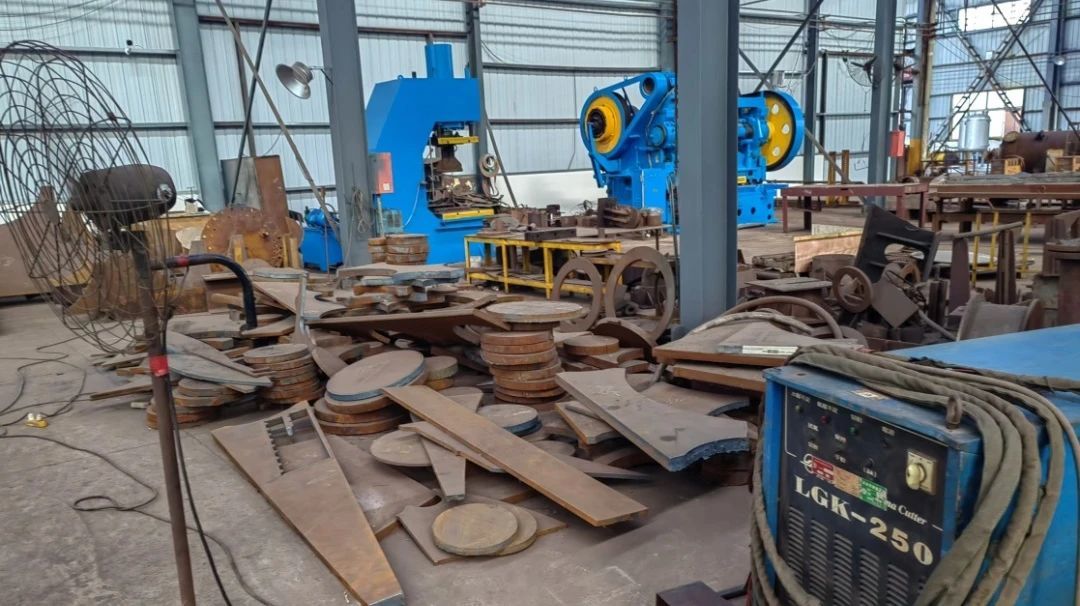
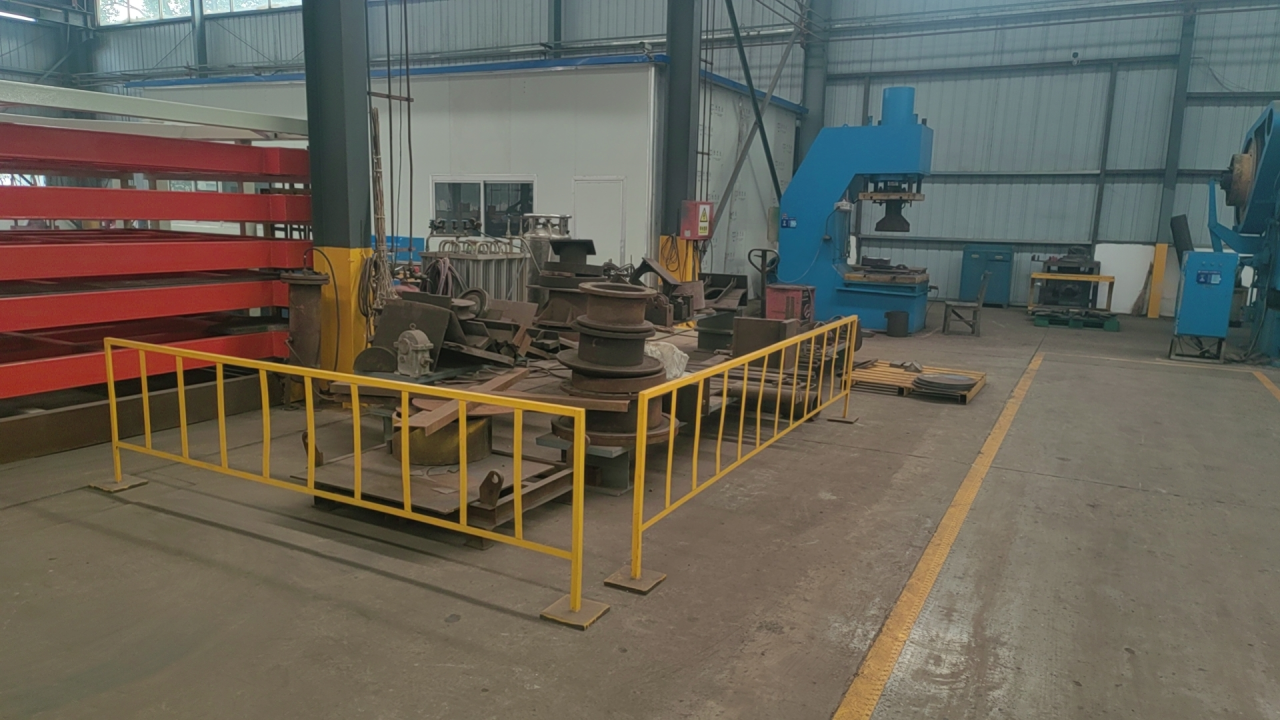
▲ The tooling for the press has been organized, discarding outdated tools that have not been used for many years, and arranging them reasonably based on usage frequency, making it clear at a glance, allowing every user to work quickly and efficiently.
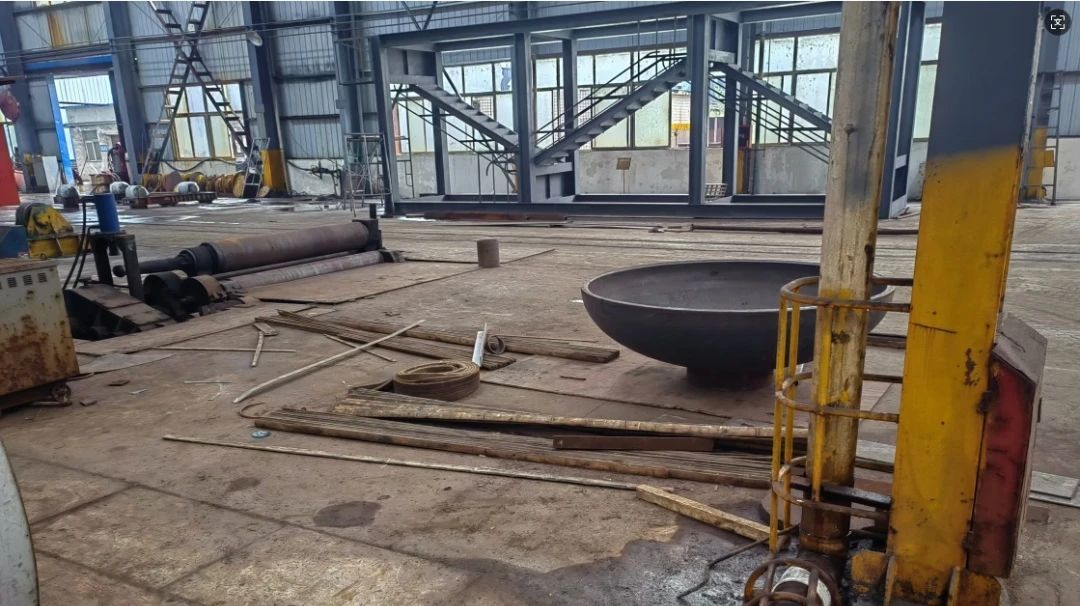
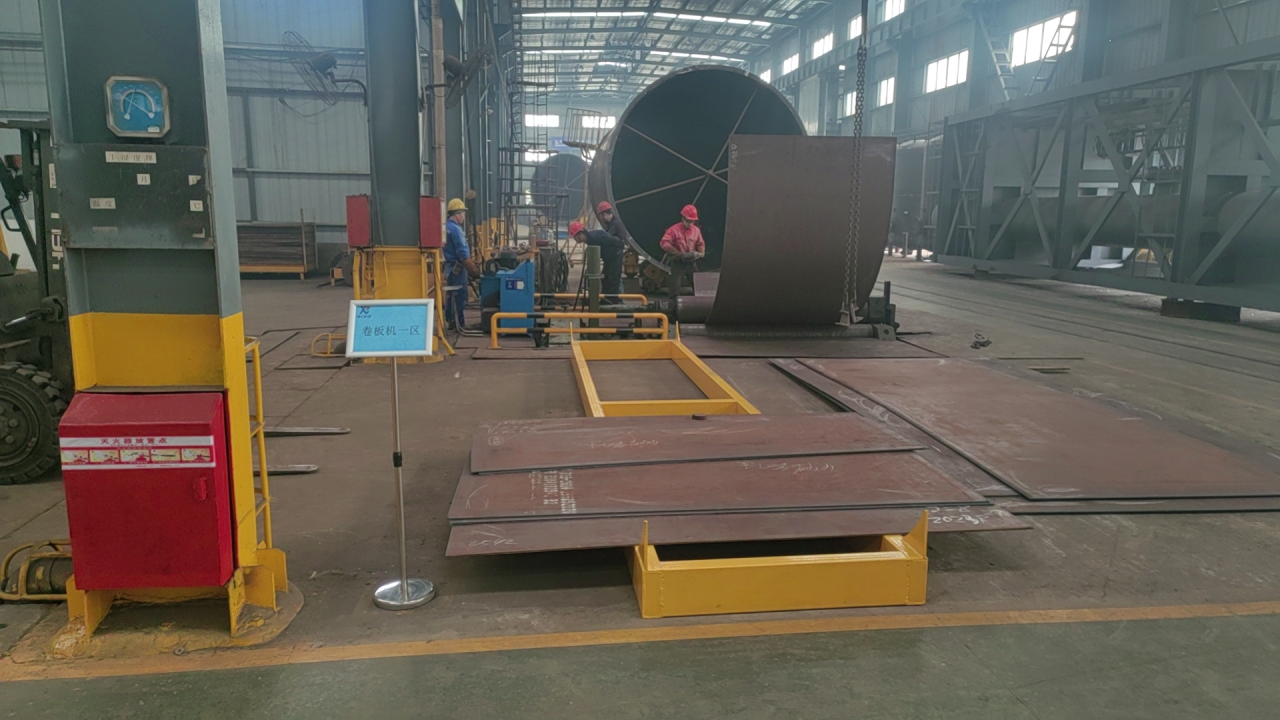
▲ Temporary placement racks have been added to improve product quality and enhance the working environment.
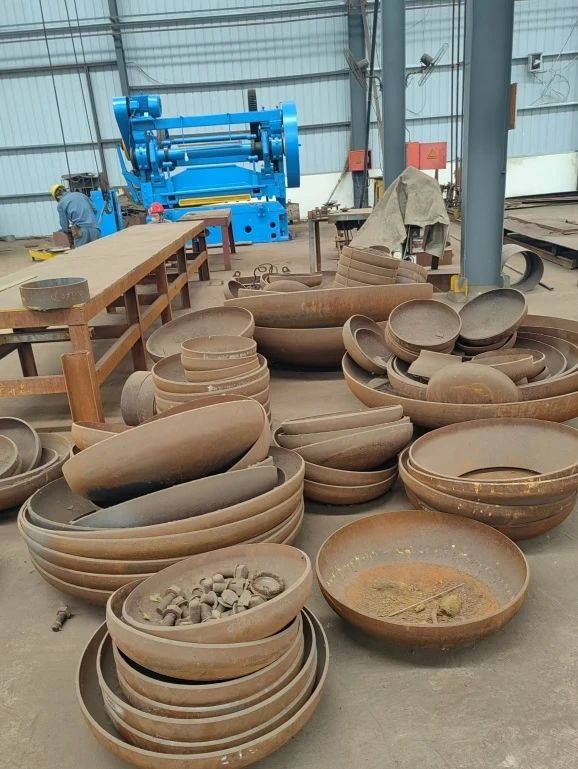
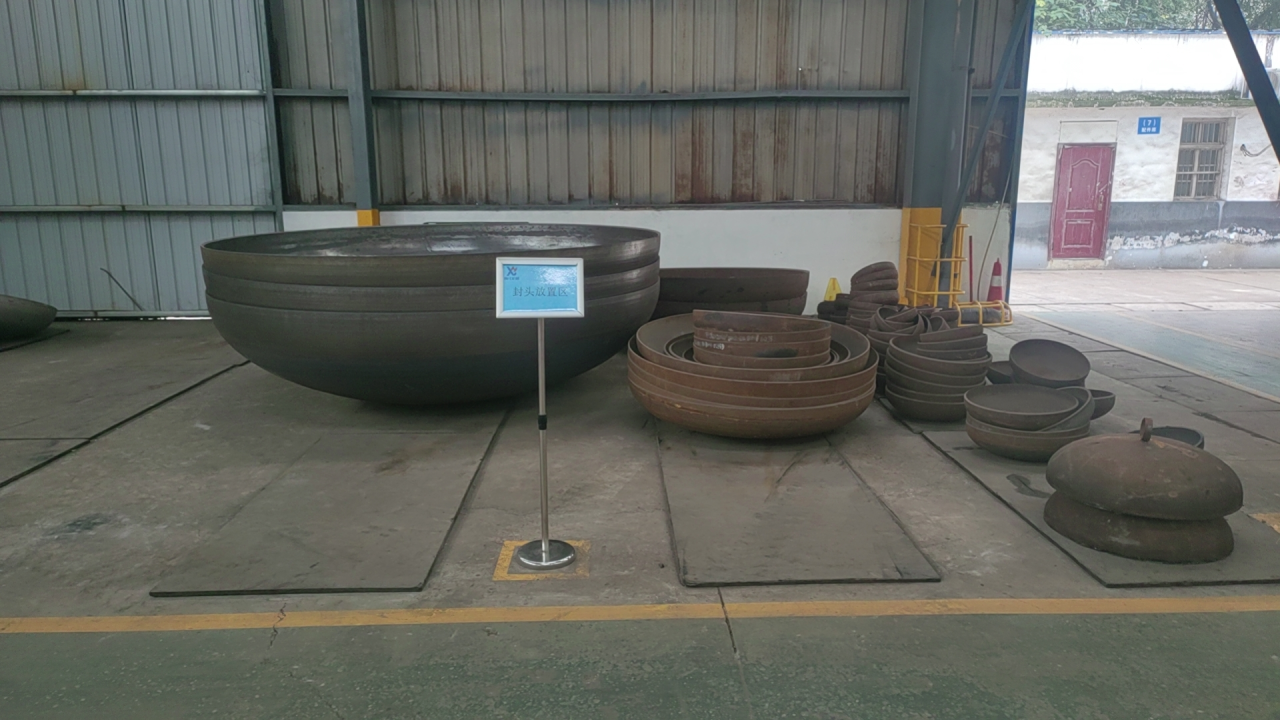
▲ The placement area for end caps has been redefined, separating carbon steel and stainless steel, categorizing them for placement, and isolating them from the ground with rubber mats for convenient and quick access.
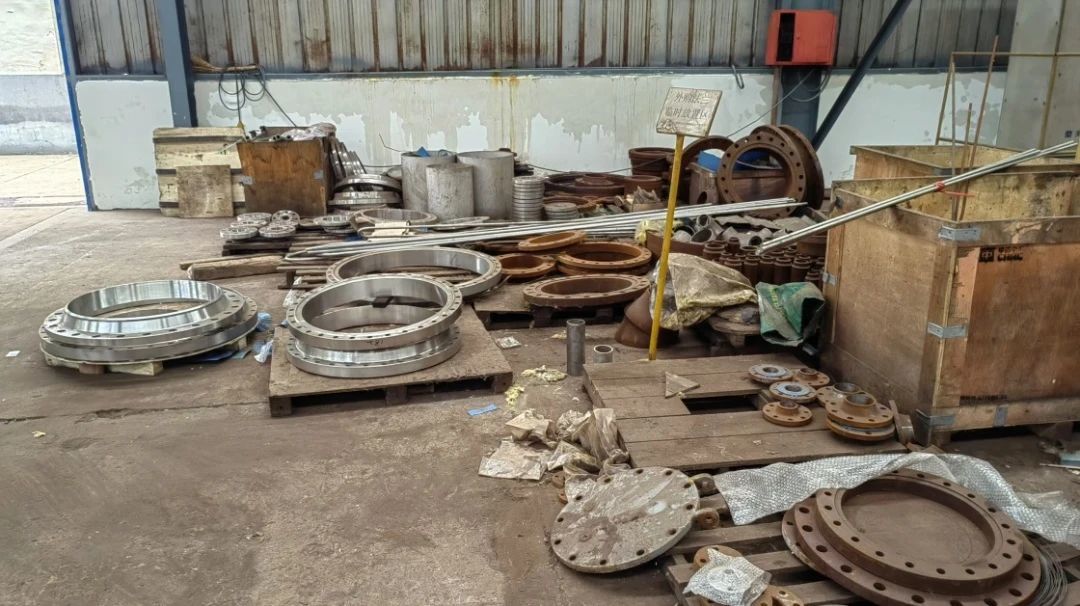
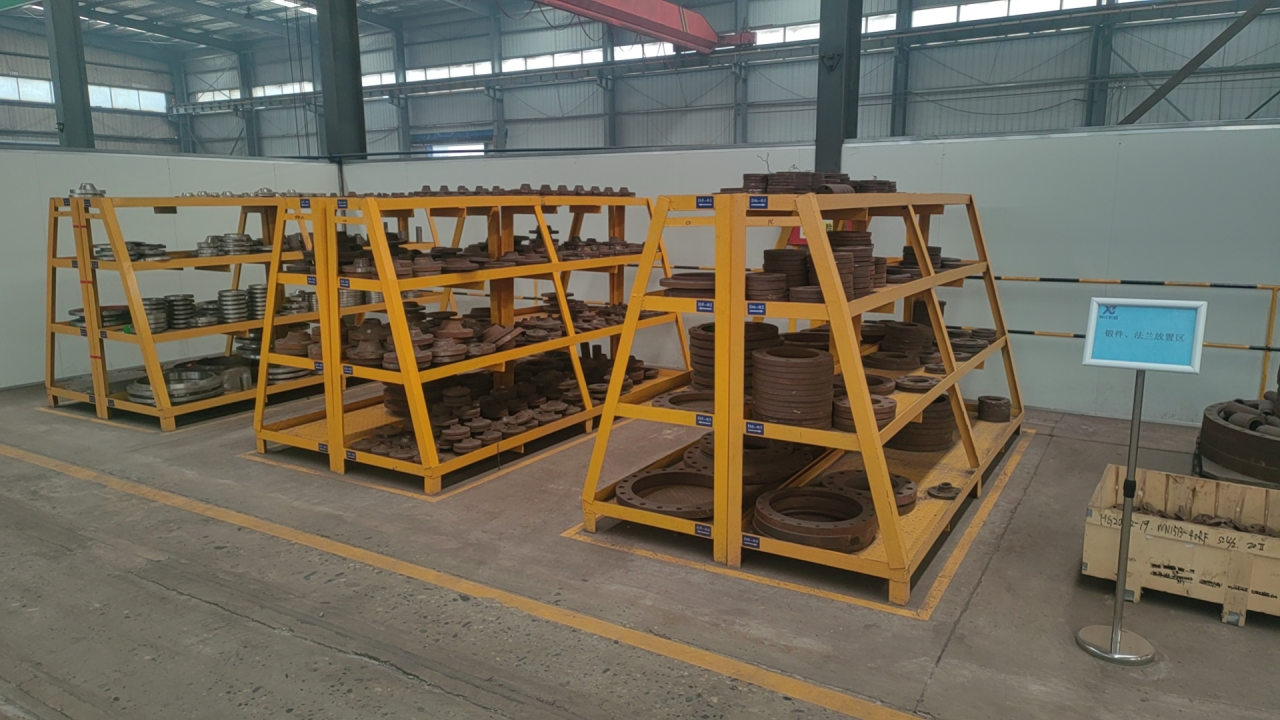
▲ The flange placement area has been organized, with layered and categorized placement, making flange retrieval "so easy!"
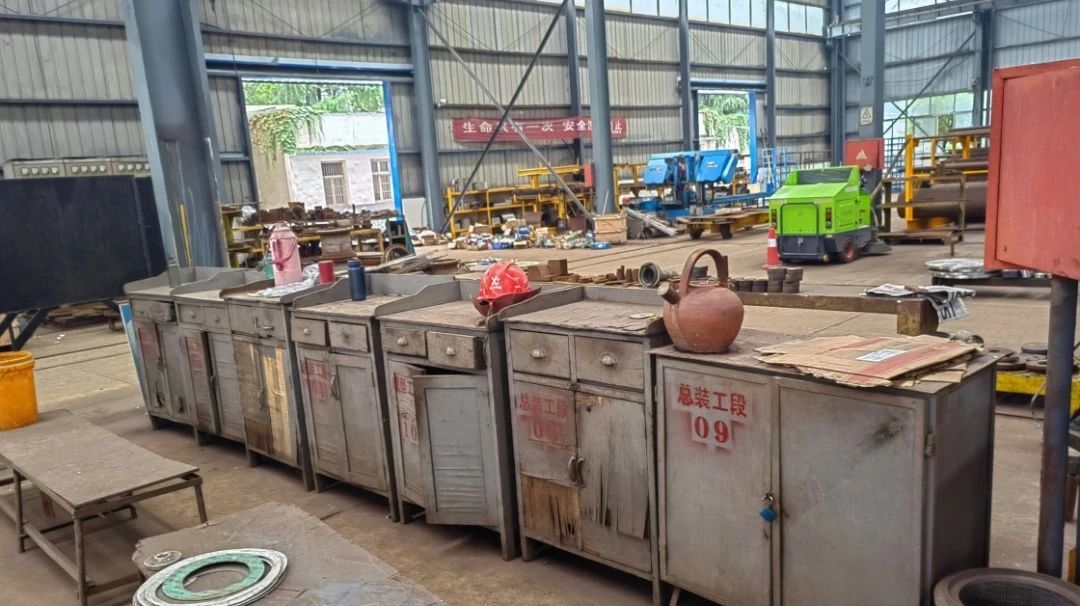
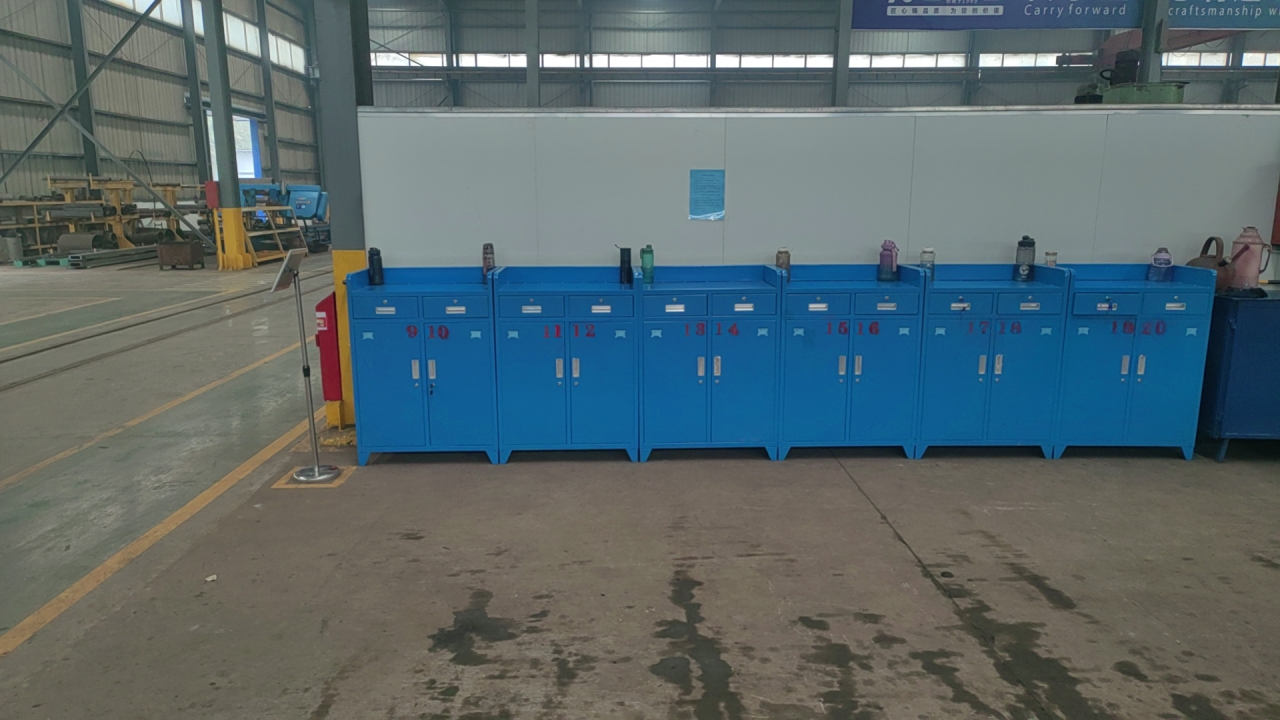
▲ Employee tool cabinets have been replaced, with humanized management providing employees with private space while creating a beautiful landscape in the workshop.
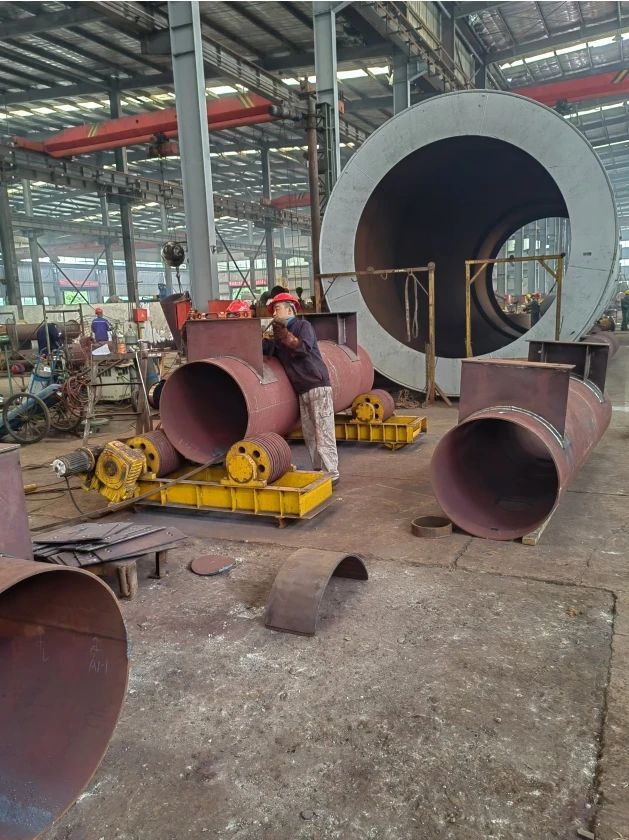
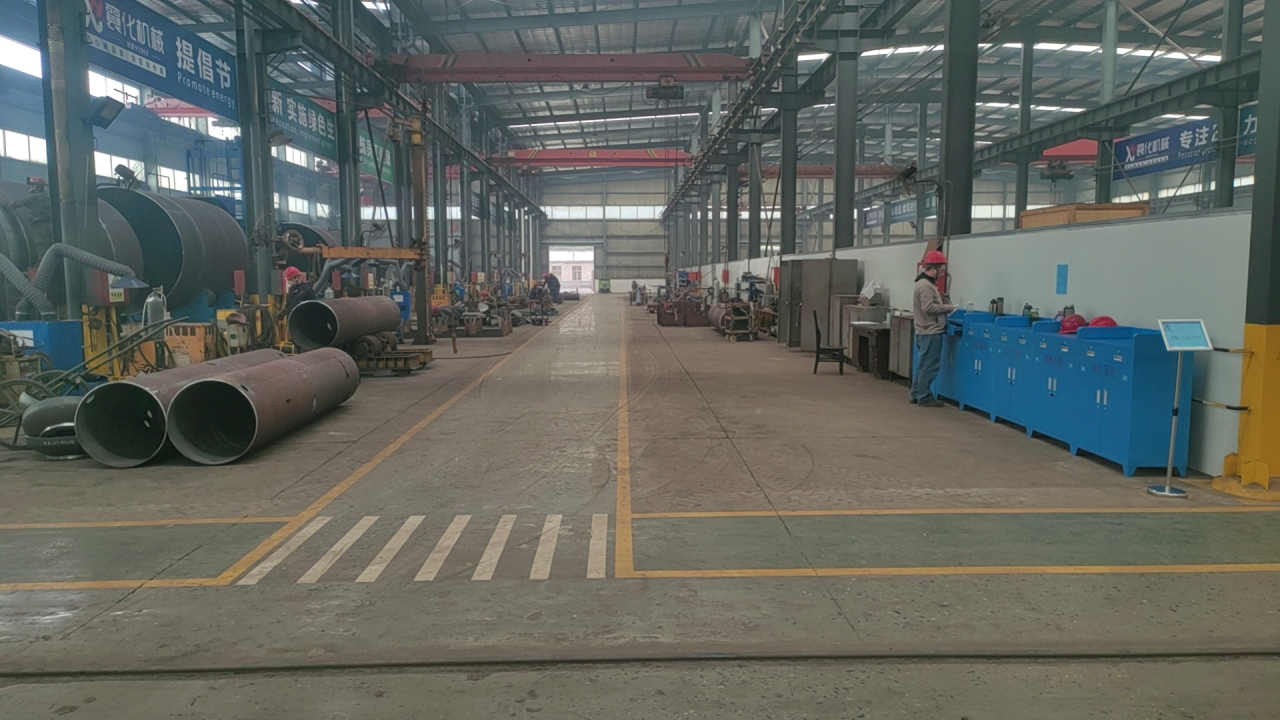
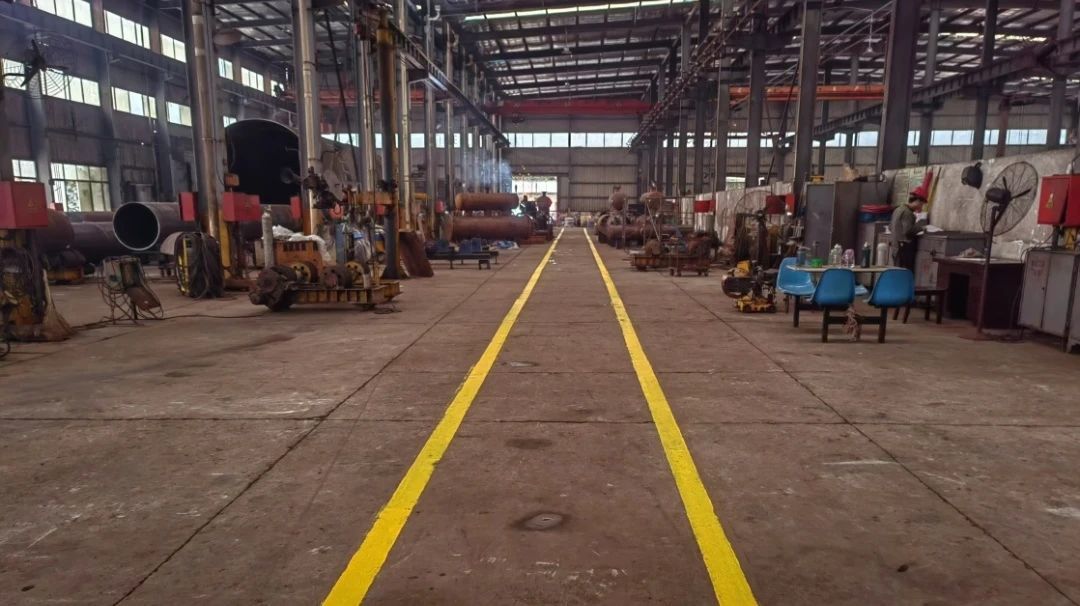
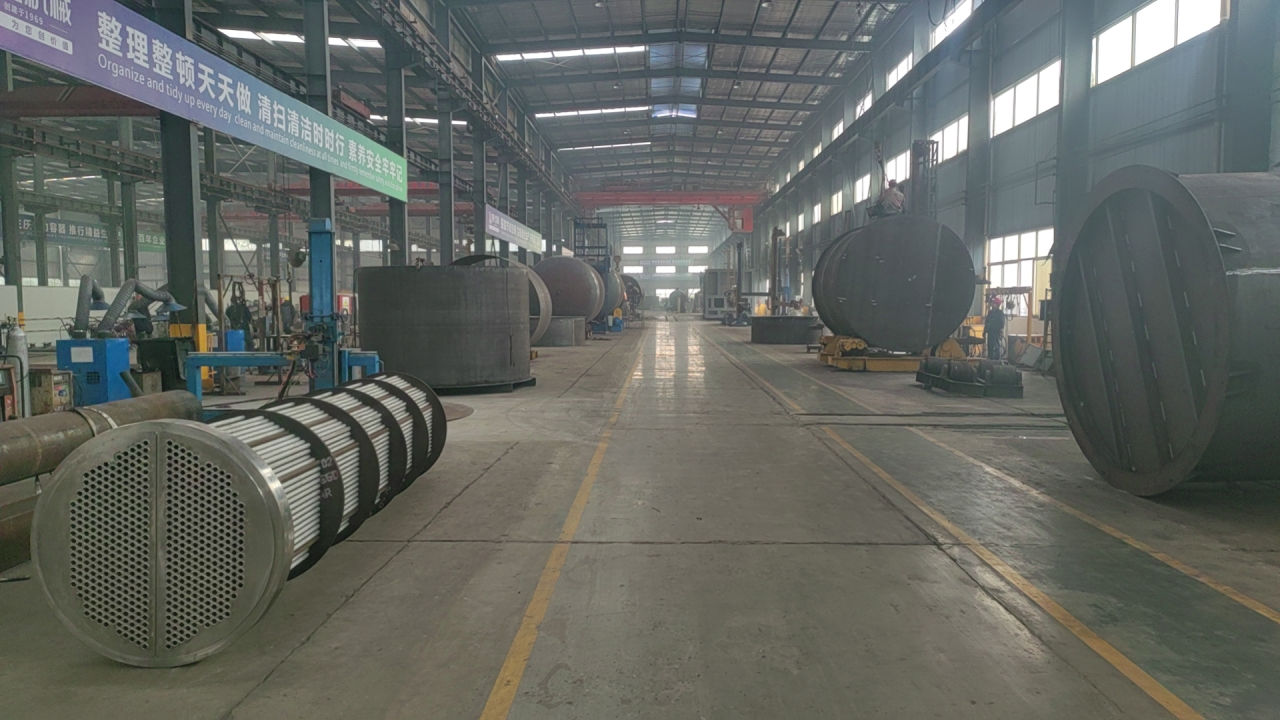
▲ Damaged floors have been repaired, painted, and marked, creating a standardized modern factory.
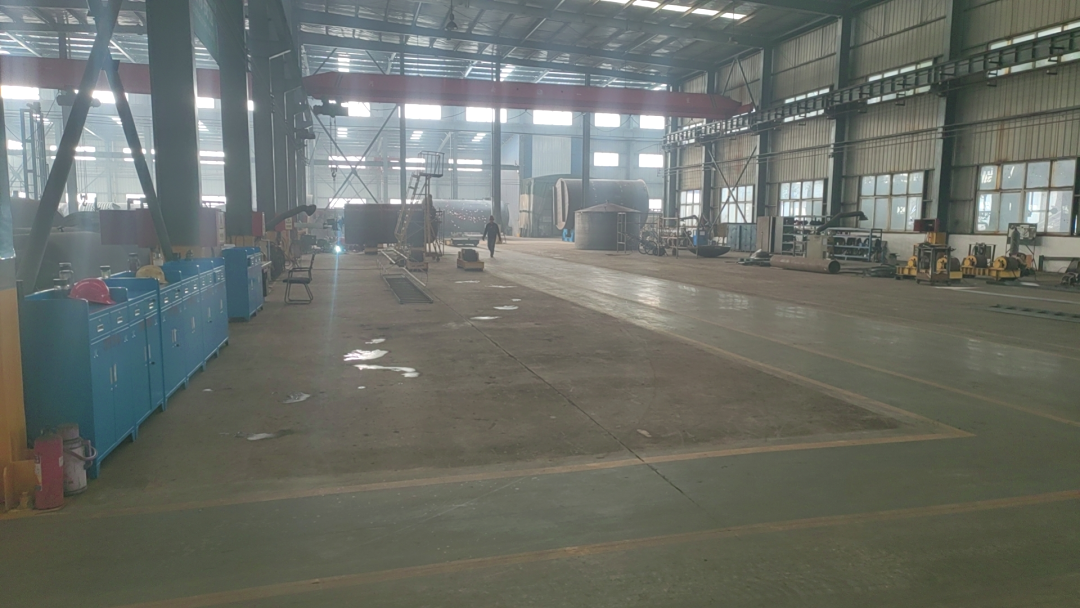
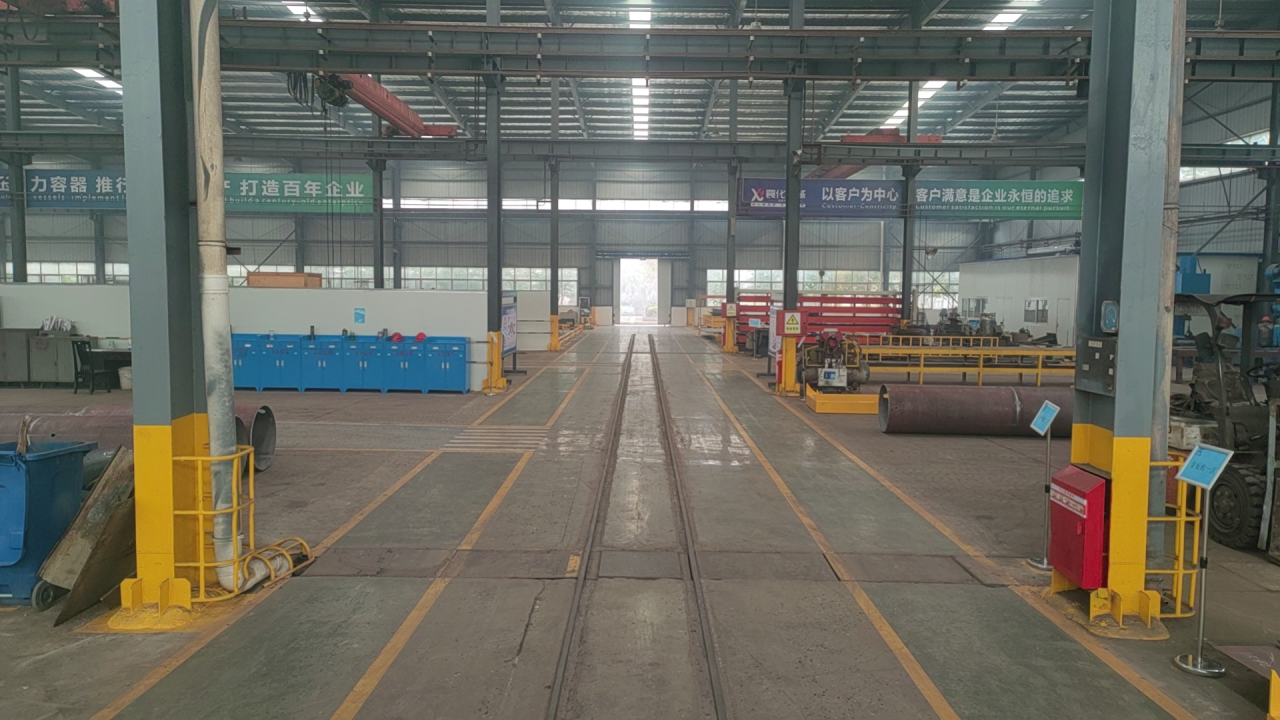
▲ Through the participation of all employees in the lean 6S activities, the entire workshop has become clean and bright, enhancing employees' sense of belonging, and striving towards the goal of a "garden-style factory!"
Continuously carry out lean control of materials on the production site.
1. All materials should not touch the ground: small materials use three-dimensional shelves, standard pallets, and turnover boxes, with fixed positioning and indexed labeling for storage; large materials and semi-finished products use standard pallets, with unique numbering for storage.
2. Implement the first-in, first-out principle for material storage: the centralized storage area for materials should be lean-planned, categorized and zoned for storage, with clear labeling, and a prominently marked first-in, first-out transfer channel should be set up, along with various tools and equipment to reduce motion waste.
3. Continuously carry out lean production activities, making small improvements to processes and equipment to enhance quality and production efficiency.
Continuously carry out 6S management on the production site.
1. For each team's workstations, develop a unified and standardized distribution map for on-site equipment, tools, and materials, and the workshop should strengthen dynamic control. Items not placed according to the distribution map must be returned to their positions before the end of each workday.
2. For each team's equipment, tools, and instruments that are not in good condition, and for safety protection and facilities that are inadequate, the safety department, equipment department, and each team in the workshop should conduct weekly safety responsibility supervision activities.
Continuously identify non-value-added activities on the production site, analyze and compare against the content and examples of the eight wastes in lean improvement, fully leverage the enthusiasm of team leaders and management personnel above the "eight major roles" in the workshop, hold brainstorming discussions for lean improvement, form improvement lists, and continue to improve; especially promote, standardize, and improve the equipment and process improvement experiences and issues raised by team leaders and skilled personnel during the equipment standard operation benchmarking exchange activities in the second half of 2024.
Keyword: Hubei Xianghua Machinery | Lean Improvement in Action (Part 1)
RELATED INFORMATION
Company Dynamics
-
Prospective clients visited Hubei Xiang Hua Machinery for inspection and exchange
Time:2025-05-10
-
"Cultivation and Application Integration" New Exploration: In-depth Cooperation Between Xiangyang Human Resources Agencies and Zhongbo Welding School
Time:2025-04-29
-
Hubei XiangHuaJi was awarded the "2024 Hubei Provincial Manufacturing Industry Single-Item Champion Enterprise"
Time:2025-04-29
-
Visit from German environmental giant! Hubei Xiang Hua Machinery wins new opportunities for localized production cooperation with its hard-core strength
Time:2025-04-09
-
The BaoKang County Employment Bureau organized a group to inspect the ZhongBo Welding Training School under Hubei XiangHua Machinery.
Time:2025-04-01
-
Laohukou Municipal Human Resources and Social Security Bureau leaders investigated Xiang Hua Machinery's Zhongbo Welding School, jointly exploring new paths for 'industry-education integration'.
Time:2025-03-25
-
Hubei Xiang Hua Machinery conducts internal training on "Organizational Growth and Efficient Execution"
Time:2025-03-14
-
The Ministry of Finance conducted a survey of Zhongbo Welding Training School, a subsidiary of Xiang Hua Machinery in Hubei Province
Time:2025-03-12
-
Hubei Xianghua Machinery demonstrates the dual responsibility of corporate strength and social responsibility, winning the favor of potential clients again.
Time:2025-02-27
-
Hubei Xianghua Machinery conducts DeepSeek application and practice training, Chairman Xiang Huailin emphasizes the opportunities and challenges of AI intelligence.
Time:2025-02-26
-
Strive for a "good start" in the first quarter, work hard to achieve excellent results.
Time:2025-02-25
-
Hubei Xianghua Machine made its appearance at the Xiangyang "Spring Breeze Action" job fair, offering over 70 quality job positions.
Time:2025-02-07
-
Hubei Xianghua Machinery undertakes the overall delivery of 300,000 cubic meters/day gas liquefaction skid-mounted equipment.
Time:2025-01-18
-
Hubei Xianghua Machinery | Zhongbo Welding Skills Training Helps Improve Skills and Increase Employment Income for the Public
Time:2025-01-14
-
Hubei Xianghua Machinery | Lean Improvement in Action (Part 1)
Time:2025-01-08
-
2025 is here with a fresh start | The official website of Hubei Xianghua Machinery has been completely upgraded and launched.
Time:2025-01-06
-
Striving for new achievements and creating a new situation | Hubei Xianghua Machinery 2024 Year-End Summary
Time:2025-01-04
-
Unwavering in our mission, we forge ahead to write a new chapter - New Year’s message for 2025 from Chairman Xiang Hualin of Hubei Xianghua Machinery.
Time:2025-01-03
-
The second welding skills competition for Xianghua Machinery interns and graduates of Zhongbo Welding School has successfully concluded.
Time:2025-01-02
-
Chairman Kang Heping of Sanbao Group and his delegation visited and exchanged ideas at Hubei Xianghua Machine.
Time:2024-12-18
-
Xianghua Machinery is fully operational in the fourth quarter, busy with deliveries, striving to achieve a 'full house' success!
Time:2024-11-18
-
The first party branch of the Human Resources and Social Security Bureau of Xiangyang City and the temporary party branch of the seventh inspection team of the municipal party committee visited for research.
Time:2024-10-28
-
Fighting for a "Year-Round Red", Hubei Xianghua is busy with multi-line operations.
Time:2024-09-29
-
The Secretary of the Party Leadership Group and Director of the Hubei Provincial Human Resources and Social Security Department came to the Hubei Xianghua Welding School for research.
Time:2024-09-27
-
Hubei Xianghua Machinery participated in the "Oil and Natural Gas Exhibition" with a focus on: the comprehensive utilization of waste mineral oil recycling and the LNG natural gas project receiving significant attention!
Time:2024-09-25
-
Hubei Xianghua Machinery will participate in the 29th Kazakhstan International Oil and Gas Exhibition in 2024.
Time:2024-09-24
-
Hubei Xianghua machinery manufacturing has taken solid steps towards high-quality development.
Time:2024-08-26
-
Stirring device of reactor manufacturer equipment
Time:2024-07-09
-
The Hubei Xianghua Machine held a kick-off meeting for the Lean Benchmark Factory Planning Project.
Time:2024-07-02
-
Hubei Xianghua organized a "July 1" themed party day event to celebrate the 103rd anniversary of the founding of the Party.
Time:2024-07-01
-
Join hands to build the "Belt and Road" and explore a new chapter of prosperous future | Hubei Xianghua Machinery visits friendly cooperative foreign trade enterprises
Time:2024-06-17
-
Introducing advanced production equipment, the orders for Hubei Xianghua Machinery are accelerating!
Time:2024-06-08
-
Hubei Xianghua Machinery and Hubei University of Technology jointly build a high-quality school-enterprise cooperation model.
Time:2024-06-01
-
Important partner from Xianghua, Hubei visits the production site to conduct a comprehensive inspection of the skid-mounted equipment production!
Time:2024-05-27
-
Hubei Xianghua Machine was invited to participate in the Hubei Province "Manufacturing Leaders" industry chain and supply chain docking event.
Time:2024-05-18
-
Hubei Xianghua Machinery Equipment signed a strategic cooperation agreement with Greeenmei for a trade-in program.
Time:2024-05-07
-
Promoting the development of new quality productivity with equipment updates | Hubei Xianghua Machine introduces a brand new automatic welding machine for edge beams
Time:2024-05-06
-
Hubei Xianghua machinery equipment is making solid progress, showcasing a new style in the pressure vessel manufacturing industry.
Time:2024-04-30
-
Empowerment through Learning | "PDCA Cycle Work Method" Training and "New Quality Productivity" Study
Time:2024-04-23
-
14 stainless steel reactors manufactured by Hubei Xianghua Machinery Equipment have been shipped.
Time:2024-04-09
-
Xianghua Machinery Equipment has completed the delivery of 3 stainless steel reactors for Hubei Benxing New Energy Company.
Time:2024-03-16
-
Xianghua Machinery Equipment has completed the delivery of 3 stainless steel reactors for Hubei Benxing New Energy Company.
Time:2024-03-08
-
Xianghua Machine held a monthly meeting to deploy and promote key work.
Time:2024-02-29
-
【Spring Festival does not stop work, striving to ensure delivery】 14 phosphorus reactors from Hubei Darun successfully delivered
Time:2024-02-19
-
湖北襄化机2024年年会暨颁奖典礼圆满举行
Time:2024-02-06
-
Technical analysis of new DMF composite solvent refining process in Hubei chemical machinery
Time:2020-06-18
-
The construction of 8 expressways in Xiangyang City is progressing in an orderly manner, which is beneficial for the development of the waste oil recycling industry.
Time:2020-06-18
-
How Hubei Chemical Machinery Strengthens the Heat Transfer Performance of Fin Tube Heat Exchangers
Time:2019-01-19
-
Enhanced heat transfer technology for shell and tube heat exchangers in Hubei chemical machinery
Time:2019-01-19
-
The general types of methods for enhancing heat transfer in Hubei chemical machinery shell courses.
Time:2019-01-19
Industry Information
-
Overview of chemical storage tank manufacturers and materials
Time:2025-04-25
-
Stainless steel liquid ammonia storage tank manufacturers
Time:2025-04-15
-
Working principle of stainless steel reaction kettle
Time:2025-04-08
-
Advantages of Material Selection by Pressure Vessel Manufacturers
Time:2025-03-31
-
Advantages of Pressure Pipeline Installation Manufacturers
Time:2025-03-24
-
Advantages of Liquid Ammonia Storage Tank Manufacturers
Time:2025-03-20
-
Application scenarios and material selection of stainless steel reaction kettles
Time:2025-03-17
-
Manufacturing Process and Standards for Pressure Vessels
Time:2025-03-07
-
The application prospects of stainless steel storage tanks in the environmental protection field
Time:2025-02-28
-
Stainless Steel Reactor
Time:2025-02-20
-
Customers interested in Hubei Xianghua machinery visited for inspection and communication, seeking to jointly explore a new chapter of development.
Time:2025-02-18
-
Stainless Steel Reactor Manufacturing Factory
Time:2025-02-12
-
Stainless Steel Tank / Pressure Vessel Manufacturing Manufacturer
Time:2025-02-08
-
Pressure vessel manufacturing factory
Time:2025-01-16
-
Chemical storage tank manufacturing factory
Time:2025-01-10
-
The working principle of a tubular heat exchanger
Time:2024-12-25
-
Safety operation procedures for pressure vessel manufacturers
Time:2024-12-17
-
Inspection items and cycles for chemical storage tanks
Time:2024-12-13
-
What are the methods for corrosion prevention of storage tanks? Construction plan for corrosion prevention of the inner wall of storage tanks.
Time:2024-12-09
-
Inspection items of chemical storage tank manufacturers
Time:2024-12-03
-
How do heat exchanger manufacturers repair corrosion?
Time:2024-11-28
-
Causes of heat exchanger corrosion
Time:2024-11-26
-
Classification of heat transfer principles in heat exchanger manufacturers
Time:2024-11-20
-
Xianghua Machinery is fully operational in the fourth quarter, busy with deliveries, striving to achieve a 'full house' success!
Time:2024-11-18
-
Advantages of stainless steel condenser manufacturers
Time:2024-11-16
-
Maintenance and Inspection of Chemical Storage Tank Manufacturers and Usage Precautions
Time:2024-11-11
-
Precautions for the manufacturing and installation of tank manufacturers
Time:2024-11-07
-
Tank manufacturer production and installation construction plan
Time:2024-11-05
-
What are the differences between horizontal tanks and vertical tanks? Which one should be chosen, horizontal or vertical tanks?
Time:2024-10-30
-
Classification of manufacturers of tubular heat exchangers
Time:2024-10-25
-
Heating methods of reaction vessels
Time:2024-10-22
-
Introduction to the function and principle of the reactor stirrer
Time:2024-10-09
-
What is the typical capacity of an LNG liquefied natural gas storage tank?
Time:2024-10-07
-
How to choose a manufacturer of stainless steel storage tanks
Time:2024-10-05
-
The lean benchmark factory project continues to advance, empowering industrial upgrades and optimizing customer value experience.
Time:2024-09-30
-
Design specifications and requirements for liquid ammonia storage tank manufacturers
Time:2024-09-24
-
What are the classifications of chemical storage tank manufacturers?
Time:2024-09-18
-
Classification of equipment for pressure vessel manufacturers
Time:2024-09-15
-
What conditions must a pressure vessel manufacturer meet to be considered a special equipment?
Time:2024-09-12
-
What are the operating conditions of pressure vessel manufacturers?
Time:2024-09-09
-
Types of safety accessories and inspection cycles for pressure vessel manufacturers
Time:2024-09-06
-
Basic requirements for material selection by pressure vessel manufacturers
Time:2024-09-03
-
The Deputy Director of the Provincial Human Resources and Social Security Department, the Secretary of the Party Committee and Director of the Provincial Labor and Employment Service Center, and their delegation visited the Xiangyang Zhongbo Welding Skills Training School under Hubei Xianghua Machine for research.
Time:2024-08-31
-
What materials are used by pressure vessel manufacturers? What is the manufacturing process of pressure vessels?
Time:2024-08-28
-
Measures taken by pressure vessel manufacturers to prevent accidents
Time:2024-08-26
-
Regular inspection content for pressure vessel manufacturers
Time:2024-08-21
-
How often should pressure vessels be inspected? What is the service life of pressure vessels?
Time:2024-08-17
-
Manufacturing process of stainless steel storage tank manufacturers
Time:2024-08-12
-
Analysis of the structure of common storage tanks by storage tank manufacturers
Time:2024-08-08
-
Safety precautions for the use of reaction vessels
Time:2024-08-05
-
The five major components of the pressure vessel shell outside the cylinder body
Time:2024-07-30
-
Theoretical Manufacturing and Main Characteristics of Pressure Vessel Manufacturers
Time:2024-07-27
-
Composition of the cylinder body in pressure vessel manufacturing
Time:2024-07-24
-
Pressure vessel equipment manufacturer
Time:2024-07-22
-
Inspection and testing standards for atmospheric pressure storage tank manufacturers
Time:2024-07-16
-
Classification of reactor equipment manufacturers
Time:2024-07-05
-
Classification and maintenance of condensers
Time:2024-06-26
-
The difference between evaporators and condensers
Time:2024-06-22
-
Precautions for Using Heat Exchanger Manufacturers
Time:2024-06-17
-
Tube-type heat exchanger - heat exchanger manufacturer
Time:2024-06-11
-
Advantages and disadvantages of floating head and U-tube heat exchangers
Time:2024-06-07
-
Classification of heat exchanger manufacturing - heat exchanger manufacturers
Time:2024-06-03
-
Basic knowledge of plate heat exchangers
Time:2024-05-30
-
Heat exchanger production process
Time:2024-05-20
-
Considerations for Choosing a Reactor Manufacturing Factory
Time:2024-05-16
-
Characteristics of the products from the manufacturer of reactor equipment
Time:2024-05-11
-
Classification of Chemical Storage Tanks - Tank Production Manufacturers
Time:2024-05-04
-
Precautions for Using Stainless Steel Reactors Produced by Pressure Vessel Manufacturers
Time:2024-04-30
-
Structural performance and advantages of stainless steel reactors
Time:2024-04-27
-
Difference between stainless steel reactors and enamel reactors
Time:2024-04-17
-
Welding between mechanical equipment components of pressure vessels
Time:2024-04-12
-
Basic knowledge of openings and pipe connections in pressure vessel shells
Time:2024-04-08
-
Pressure vessel combined cylinder and sealing device
Time:2024-03-29
-
Introduction to Single-Layer Cylindrical Pressure Vessels
Time:2024-03-26
-
Basic structure of pressure vessel equipment manufacturing
Time:2024-03-21
-
Installation process and construction key points of pressure pipelines
Time:2024-03-14
-
Requirements for the safety technology of pressure vessels
Time:2024-03-09
-
The difference between single-layer and double-layer enamel reaction kettles
Time:2024-03-05
-
What is a pressure vessel? What are the precautions for using pressure vessels?
Time:2024-02-29
-
Safety management of mechanical engineering equipment
Time:2024-01-31
-
Seven Major Safety Supervision Guidelines for Pressure Vessel Special Equipment
Time:2024-01-22
-
Product features of stainless steel reaction kettle
Time:2024-01-10
-
What types of stainless steel tanks are there for pressure vessel equipment?
Time:2023-12-28
-
Chemical machinery - Manufacturing demand for storage equipment for hazardous waste enterprises that regenerate waste oil into base oil.
Time:2020-07-11
-
Design Principles for Hazardous Waste Storage Facilities for Comprehensive Utilization of Waste Mineral Oil
Time:2020-06-30
-
Requirements for the site selection of storage facilities for waste oil regeneration base oil enterprises
Time:2020-06-27
-
Chemical Machinery - The first promotion meeting of the Green Full Xiangyang Re-Upgrade Action in Xiangyang City was held.
Time:2020-06-27
-
Chemical machinery - disposal and utilization of waste mineral oil, common illegal activities
Time:2020-06-23
Exhibition style
-
Exhibition style
Time:2024-11-21
-
Exhibition style
Time:2024-11-21
-
Exhibition style
Time:2024-11-21
-
Exhibition style
Time:2024-11-21
-
Exhibition style
Time:2024-11-21
-
Exhibition style
Time:2024-11-21
-
Exhibition style
Time:2024-11-21
-
Exhibition style
Time:2024-11-21
-
Exhibition style
Time:2024-11-21
-
Exhibition style
Time:2024-11-15
-
Exhibition style
Time:2024-11-15
-
Exhibition style
Time:2024-11-15
-
Exhibition style
Time:2024-11-15
-
Exhibition style
Time:2024-11-15
-
Exhibition style
Time:2024-11-14